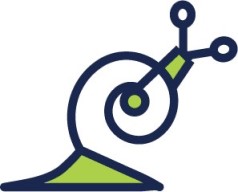
シャシーの構造強度評価をモデル化したデータに入力を加えた時の変位をFEMで解析する手法は世界中で行われている。このモデル化が不正確である場合解析が導く結果の信用性が疑われることもままある。解析の対象が部分的であるので対象外の構造との境界条件に関する人為的な仮定が不正確である場合や入力の大きさと方向の組み合わせが実態から乖離していることなどが原因である。このためある大手のOEMの解析チームは一部切り出しモデルの使用を禁じていた。また、モデルとばらつきを持つ実体の違いから応力集中を見誤り実体の破損を予知できないこともある。CAEを徹底して将来実験不要の開発をするという夢が語られることやベンチャー企業がCAEを過信して試験を省略しようなどと考えがちであるが、CAEを開発プロセスで活用するためにはあらかじめ実験結果との相関性を熟知する必要がある。
トラックの設計チームにおいては、主要なコンポーネントの設計及び維持管理よりもその周辺の様々な付帯部品の種類の管理であリこれに要する工数が頭の痛い問題である、
付帯部品には小物のブラケットや電線、パイプ類 ホース類がある。
オプション部品が複雑に構成されていて,その組み合わせや両立性の有無などが絡み合って収拾のつかない状況になっている事がある。欧州ではこのパズルに取り組むのは若い技術者であり日本では設計外注の会社のようである。コロナ禍ではエッセンシャルワーカーに皺寄せが行っているような状況がトラックの設計でもあると言える。付加価値が低いと思われているのに手間が異常にかかるいわゆる汚れ仕事と位置付けられているためモチベーションの維持が難しく作業者の定着率も低い傾向がある。
トラック業界は寡頭競争に晒されていて利益率が低く、顧客確保のために多岐のバリエーションを揃えて満足度を得る努力に しのぎを削っている。このことがこの問題の背景である。
モジュール設計というのはボルボやフォードが熱心に提唱してきた設計の概念である。中間的な共通の塊を作ってそれを組み合わせられるようにあらかじめ設計しておくことによって、全体の種類は多岐にわたる顧客の要望に答えながら、それぞれのモジュールは数種類しか持たないということが理論上可能という理念である。
別の章で論じたフレームのグリッドパターンもその一環である。
開発マネージメントの大きな課題と言える。
トラックのシャシーにおいてボルトの緩みはしばしば問題になる。
ある海外の野心的な業者のセルフロックナットのカタログを見たことがあるが
低い締め付けっトルクで緩み止め効果ありと謳っていた。
原理はネジ部の変形のしかたに特長ありとのことである。
締め付け時の抵抗が大きく、さらにトルクを制限しているので軸力確保に不安があると思われたので通常の標準品に戻して締め付けトルクをボルトの降伏限界まで上げることを設計者にリコメンドした。その業者のセルフロックナットで緩みの不具合が絶えなかったためである。
一般的にボルト締め付けにおいてエアインパクトを使用している場合が多い。
この場合、締め付けトルクのばらつきが比較的大きい。
このため設計図上の規定を無視して現場判断で上限を超えるトルクで締め付けている場合が見受けられる。実質的に塑性域に入るが経験上実害がないとされていると思われる。
欧州のある企業は降伏点まで締め付けトルクで軸力を上げてその後さらにある角度強制的に締め付ける方法をとっていた。アメリカではHUCKボルトというシステムがあり、油圧機器で軸力を強制的に直線的に与える方法をとっている。
緩みといえば回転方向のみに目が向けられて対応を誤ることがあるが本質は被締結物のヘタリによリクランプ力が落ちることが主因であることが多い。
トラックのサイドレールには様々な用途の小穴が必要である。
また、トラックには様々な用途があり必要な穴の種類が多い。
大型トラックは従来フレーム付きのシャシー状態で工場から出荷されることがほとんどで一般的にはユーザーに渡る前の中間状態がトラックメーカーの製品である。
この中間状態に対して架装メーカーが様々な架装を施す。架装要領書で注意時事項を規定しているが時には不適切な架装によってフレームに亀裂などの不具合が発生することがある。
フレームの亀裂不具合の原因は様々であるがトラックメーカーは極度にそれを恐れる傾向がある。
恐れるあまり昔から設計においてサイドレールに捨て穴を残すななどという掟を設定することがある。
捨て穴とは締結に使用されないで種類削減のために余分に空いている穴で理論的には応力が集中する恐れがあるとされている穴のことである。
VOLVOやDAIMLERと提携した日本のトラックメーカーはグリッドパターンという考え方を導入した。
設計の初期段階で穴のパターンをあらかじめ決めておいて、詳細設計時にその中から使える穴を使い使わない穴はそのままにしておく方式である。
この処置のために設計の煩雑さが大いに軽減されたが、サイドレールウエブ面の捨て穴に応力集中が起きて破損したという事例はないと思う。
中国がまだ開発途上にある1980年代、三菱グループが対中大型商談を成立させて大型トラックの
輸出を開始したもののフレームなどの不具合が続出して数百億円規模の賠償金を払わされた事件がありました。数次にわたる”対策”は亀裂部の補強策で不具合箇所が次々と移動するだけで改善には至らなかったと推察します。当時は、何か人為的な破壊かとの説やとんでもない悪路走行かとか噂されていました。
事件が落ち着いた後フレームの設計に対する考え方を整理して改善策を恒久対策としています。
原因を整理すると、従来のように、大きな力の入力に対して剛性増大のみで対処するという対応が必ずしも有効ではなかったということです。力の大入力ではなく路面の大変異に起因する入力に対処すべきであったということです。具体的には悪路走行時にフレームにねじり変異が入ってサイドレールとクロスメンバーのボルトなどでの締結部に高応力が発生したと思われます。サイドレールは竪壁(ウエブ面)と水平面(フランジ面)とで成り立っていますが、従来、横渡し部材(クロスメンバー)との締結をフランジ面に設置して簡素化を図っていましたが、この構造では締結部に複雑な変形モードが発生します。これが高応力につながったと想定されます。正解はクロスメンバーをウエブ面に締結するということです。
インドネシア輸出で実績のあった小型トラックの設計はこのような変形モードにすでに対処しておりました。また欧米の大型トラックも対処済でした。当時の日本の大型トラックメーカーはまだどこも未対応でしたが現在は主要なメーカーは対応済です。ベンチマークをお家芸とする中国製のトラックも現在対応済で今やデファクトスタンダードとなっています。